How to make inside LSAW pipe and SSAW pipe uniform and smooth?
Release time:
2024-09-14
Longitudinal submerged arc welded pipes(LSAW PIPE) and Spiral submerged arc welded pipes(SSAW PIPE) are widely used in oil and gas transportation and building construction. But due to the welding, the interior of LSAW pipe and SSAW pipe is not always uniform or smooth, which can negatively impact its performance and durability. LEFIN STEEL mainly produces the LSAW PIPE and SSAW PIPE.
How to make inside LSAW pipe and SSAW pipe uniform and smooth?
Longitudinal submerged arc welded pipes(LSAW PIPE) and Spiral submerged arc welded pipes(SSAW PIPE) are widely used in oil and gas transportation and building construction.
But due to the welding, the interior of LSAW pipe and SSAW pipe is not always uniform or smooth, which can negatively impact its performance and durability. LEFIN STEEL mainly produces the LSAW PIPE and SSAW PIPE.
Contact: Nina Wang
Whatsapp: 008618892236531
Email: nina@lefinsteel.com
Longitudinal submerged arc welded pipes are widely used in oil and gas transportation and building construction. SSAW PIPE is a pipe material commonly used in the oil and gas, water resources and construction industries. But due to the welding, the interior of LSAW pipe and SSAW PIPE is not always uniform or smooth, which can negatively impact its performance and durability.
Generally speaking, we have a variety of methods to make the interior of the longitudinal submerged arc welded pipe more uniform and smooth after production to ensure its optimal performance.
LSAW PIPE:
Standard and grade:
Standard: EN10219, EN10217, ASTM A252, ASTM A572, API5L
Grade: S235JRH, S275JRH, S355JRH, S355J0H, S355J2H, GR.1, GR.2, GR.3, GR.A, GR.B, GR.C, X52, X80
Size: 245-1420MM
Thickness: 10-50MM
Coating: FBE Coating, 3PE Coating, 3LPE Coating, 3PP Coating, 3LPP Coating, oil painting, black varnish coating
Processing process:
1. Prepare the steel plate and cut it into the required size and shape. The JCOE process is used to press the steel plate into J shape, then C shape, and finally into O shape for welding.
2. After the weld is formed, cool the pipe and remove excess material.
3. Conduct visual inspection, flaw detection and other inspections on the pipeline to ensure that it meets the required standards.
4. Apply a protective layer to prevent corrosion. Including 3PE coating, 3LPE coating, FBE coating, etc., and then transport the pipeline to the destination
Methods:
1. Use a mandrel. Mandrels are typically made from a hard, durable material, such as stainless steel, and are designed to match the shape and size of the pipe being produced. A mandrel is inserted into the pipe during the manufacturing process to shape and smooth the inner surface. As the tube forms, the mandrel is forced through the interior, creating a uniform and smooth surface.
2. Burr removal tools are usually made of high-quality materials such as tungsten carbide and can be firmly installed inside the pipe. Burr removal tools can be used to remove any rough edges or protrusions present on the inner surface of the pipe. These tools ensure thorough and effective cleaning.
3. Check the pipeline regularly during the production process to identify any defects or abnormalities that may exist. Try to ensure smooth internal pipes during production through this method.
Advantages:
1. Longitudinal submerged arc welded pipe has high strength and durability and is suitable for a wide range of applications. They are manufactured from high-quality steel and welded to ensure the pipes are strong, reliable and resistant to damage.
2. Longitudinal submerged arc welded pipes can be manufactured in large diameters, have relatively good tensile strength and yield strength, and reduce the risk of deformation and rupture compared with ordinary pipes. They are very suitable for applications that require the transportation of large amounts of fluid or gas.
3. The manufacturing cost of straight seam submerged arc welded pipes is lower than other types of pipes, and the welding process is highly automated, reducing production costs.
4.Long seam submerged arc welded pipe can be easily installed using standard welding techniques, reducing installation time, making it a popular choice for many construction projects.
Application:
1. Oil and gas transportation: SSAW pipes are widely used in the transportation of oil, gas, and other fluids in the oil and gas industry due to their high resistance to corrosion and ability to withstand high pressure.
2. Water and sewage transportation: SSAW pipes are commonly used in water supply and sewage systems for their high durability and resistance to corrosion, making them suitable for underground and underwater applications.
3. Piling and construction: SSAW pipes are used in construction projects for piling and structural support due to their high strength and ability to withstand heavy loads.
4. Structural applications: SSAW pipes are used in various structural applications such as bridges, buildings, and tunnels for their high strength and durability.
5. Offshore and marine applications: SSAW pipes are used in offshore oil and gas platforms, marine structures, and underwater pipelines due to their corrosion resistance and ability to withstand harsh marine environments.
6. Mining and geothermal applications: SSAW pipes are used in mining operations and geothermal energy projects for their high strength and resistance to corrosion, making them suitable for harsh underground conditions.
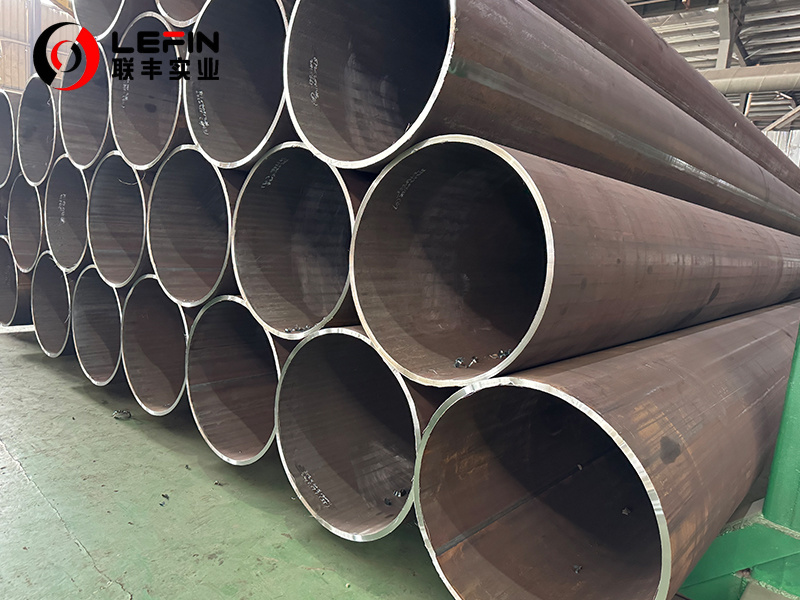
SSAW PIPE:
Standard and grade:
Standard: EN10219, EN10217, ASTM A252, ASTM A572, API5L
Grade: S235JRH, S275JRH, S355JRH, S355J0H, S355J2H, GR.1, GR.2, GR.3, GR.A, GR.B, GR.C, X52, X80
Size: 420-1420MM
Thickness: 10-50MM
Coating: FBE Coating, 3PE Coating, 3LPE Coating, 3PP Coating, 3LPP Coating, oil painting, black varnish coating
Processing process:
1. Purchase and select raw materials for spiral submerged arc welded pipes. Cut the material to the appropriate size and shape based on the required pipe specifications.
2. The pipe is formed using spiral welding technology, a process that ensures the pipe has a consistent diameter and thickness throughout its length.
3. After the welding process is completed, the pipeline undergoes a series of tests and inspections such as non-destructive testing, ultrasonic and magnetic particle testing, tensile testing and yield testing to ensure its quality and durability.
4. Coating and painting the finished spiral submerged arc welded pipe to protect it from corrosion and other environmental factors.
Methods:
1. Using advanced welding technology and equipment, operators can avoid potential defects and strive to ensure internal smoothness during the welding stage.
2. Before welding, thoroughly clean the inside of the pipe to remove any debris or contaminants.
3. Use appropriate abrasive tools to smooth out any irregularities in the weld and create a uniform surface finish
4. The inside of the pipe must be inspected to ensure it meets the required standards. This can be done visually or by non-destructive testing methods such as ultrasonic or radiographic inspection.
Advantages:
1. Spiral submerged arc welded pipes are made of high-quality steel and are strong and durable. Able to withstand high pressure, vibration and stress.
2. Spiral submerged arc welded pipes are used in a wide range of applications, including oil and gas transportation and structural applications.
3. Easy to install: Spiral submerged arc welded pipe is easy to install, making it a popular choice for projects that require quick installation, such as emergency repairs and maintenance.
Application:
1. Oil and gas transportation: SSAW pipes are commonly used in the transportation of oil and gas over long distances. They are durable, cost-effective, and can withstand high pressure and harsh environmental conditions.
2. Water transmission: SSAW pipes are also used for the transmission of water in municipal water supply systems, irrigation projects, and industrial water supply networks.
3. Construction and structural applications: SSAW pipes are often used in construction and structural applications, such as building foundations, piling, bridges, and road crossings. They provide excellent strength and stability for these applications.
4. Piling and foundation works: SSAW pipes are commonly used in piling and foundation works for buildings, bridges, and other structures. They are able to withstand heavy loads and provide stability for the foundation.
5. Offshore applications: SSAW pipes are used in offshore oil and gas platforms, as well as in offshore wind farms. They are able to withstand the harsh conditions of the marine environment and provide reliable support for these structures.
6. Transmission of chemicals and corrosive fluids: SSAW pipes are often used in the transmission of chemicals, corrosive fluids, and other hazardous materials. They are resistant to corrosion and can safely transport these substances without any risk of leakage.
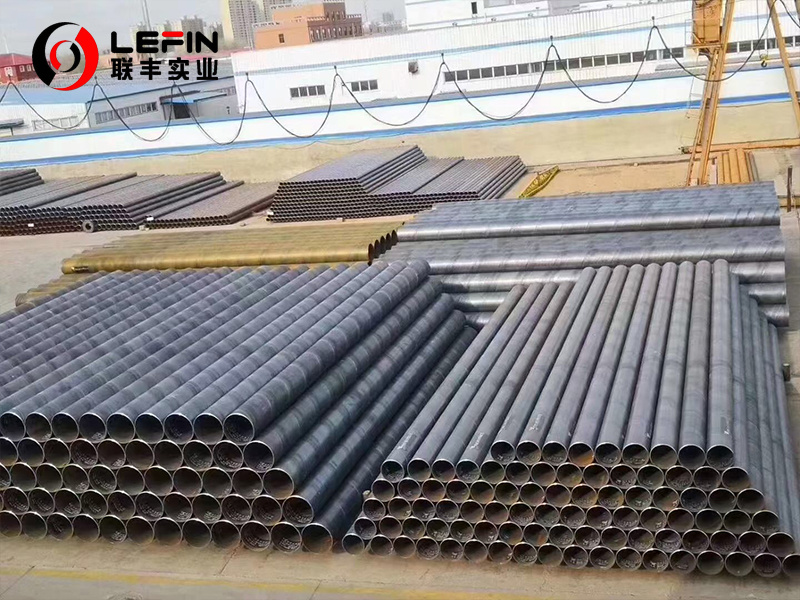
Differences between LSAW PIPE and SSAW PIPE:
1. Straight seam welded pipes are more suitable for transporting fluids and gases over long distances, while spiral submerged arc welded pipes are more suitable for transporting fluids and gases over short distances.
2. LSAW pipe is more durable and stronger, while SSAW pipe is easier to install and can be used in tight spaces.
In summary, longitudinal submerged arc welded pipes(LSAW PIPE) and spiral submerged arc welded pipes(SSAW PIPE) have different strengths and advantages, and they are both important components in the oil and gas industry and other industries.
Tags:
Relevant Project

Address: Hengtai Road,Daqiuzhuang Town,Jinghai County,Tianjin,China
Mob: +8615122229899(whatspp)
Phone: +86 22 58171905
Fax: +86 22 58171902
E-mail:info@lefinsteel.com
Get company updates

Tianjin Lefin Industrial Co.,Ltd. All rights reserved City sub-station SEO www.300.cn