What are welded pipes
Release time:
2024-09-04
Welded pipes are pipes that are manufactured by welding the edges of steel plates or coils to form a cylindrical shape. This process involves joining two or more pieces of metal by applying heat and pressure, creating a strong and durable bond at the seam. Welded pipes are mainly divided into two categories, resistance welding and spiral welding. LEFIN STEEL can produces steel pipes including ERW pipes and SSAW pipes.
What are welded pipes
Welded pipes are pipes that are manufactured by welding the edges of steel plates or coils to form a cylindrical shape. This process involves joining two or more pieces of metal by applying heat and pressure, creating a strong and durable bond at the seam. Welded pipes are mainly divided into two categories, resistance welding and spiral welding. LEFIN STEEL can produces steel pipes including ERW pipes and SSAW pipes.
Types of Welded Pipes:
ERW Pipes: These are made using the electric resistance welding process. ERW pipes are widely used in various applications such as water pipelines, structural supports, and industrial piping systems.
SAW welded: Submerged arc welding (SAW) is a welding process in which an electric arc is immersed beneath a layer of granular flux. This protects the arc from atmospheric contamination and produces high-quality welds.
Quality and Standards:
Welded pipes must meet specific standards and quality requirements to ensure they are capable of withstanding the intended pressure, temperature, and environmental conditions.
The following are commonly used standards:
1.ERW PIPE:
CHS: EN10210, EN10219, EN10255, ASTM A53, ASTM A500, BS1387, JIS G3444
RHS&SHS: EN10210, EN10219, ASTM A500, ASTM A501, MS1462, JIS G3466
LSAW Pipes: EN10210, EN10217, EN10219, ASTM A572, ASTM S53, API5L
2.SAW PIPE:
SSAW Pipes: EN10217, EN10219, ASTM A252, ASTM S53, API5L
LSAW pipes(Big sizes): EN10210, EN10217, EN10219, ASTM A572, ASTM S53, API5L
Contact: Nina Wang
Whatsapp: 008618892236531
Email: nina@lefinsteel.com
Manufacturing Process:
1. Electric Resistance Welding (ERW): This is the most common method for manufacturing welded pipes.
1. Select raw material steel coils according to the required standards, conduct quality inspection of the steel, and then uncoil.
2. The steel strip is passed through a series of rollers, which gradually bend it into a cylindrical shape, forming an elongated tube (also called a steel pipe).
3. Uses a combination of heat and pressure to form the welded seam. Electrical current is passed through the edges of the steel strip, heating them to a point where they can be joined together.
4. Pass the sizing roller and straightening roller to ensure that it meets the specified diameter and straightness requirements. Further processing is carried out to obtain final dimensions.
5. Use a saw or welding gun to cut the welded pipe to the required length.
6. Conduct non-destructive testing (e.g. ultrasonic testing, radiographic testing) to detect any defects in the weld or the pipe itself.
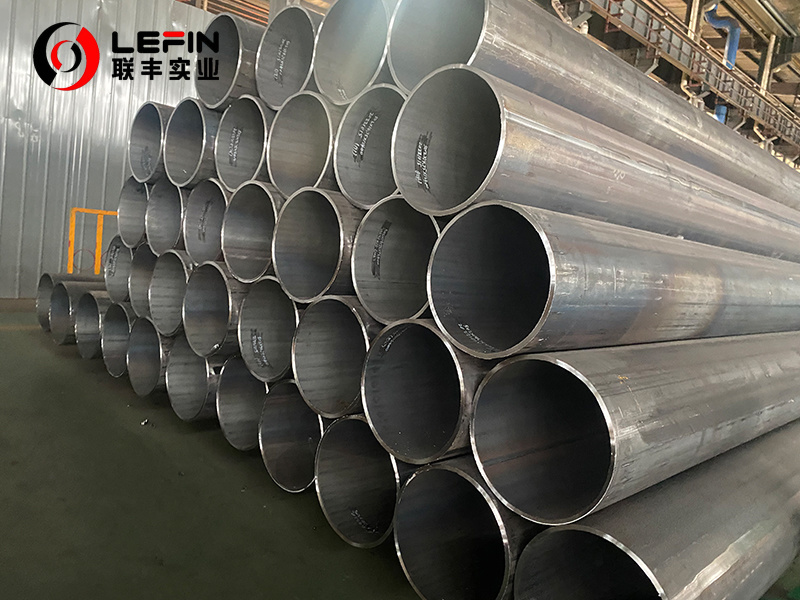
2. Submerged Arc Welding (SAW): This method involves welding the seam of the pipe using a submerged arc welding process. A granular flux is used to protect the weld zone from contamination, and the arc is submerged beneath the flux layer. SAW is typically used for thicker pipes and for manufacturing larger diameter pipes.
1. Select the appropriate steel plate or coil according to the required specifications of the pipeline.
2. Use a series of forming rollers or a bending machine to shape the prepared steel plate into a cylindrical shape.
3. The edges of the steel plates are precisely aligned to ensure they are joined correctly during the welding process.
4. Position the tube blank on a welding mandrel or rotating roller system to rotate during the welding process.
5. The welding process is carried out along the length of the tube blank, continuously connecting the edges together to form a strong weld. The heat from the arc melts the edges of the steel plates, fusing them together to form a single piece of metal.
6. After welding, the welded pipe passes through the cooling zone, heat-affected zone (HAZ) and weld metal to gradually cool down.
7. After welding, excess weld material and any irregularities are trimmed away and the pipe is sized to meet the required size and specification.
8. Perform ultrasonic testing or visual inspection to detect any defects or inconsistencies in the weld.
9. Pipe ends can be beveled to facilitate welding fittings or better joint preparation.
10. Surface treatment: Surface treatment such as painting or coating is applied to the pipe according to the application.
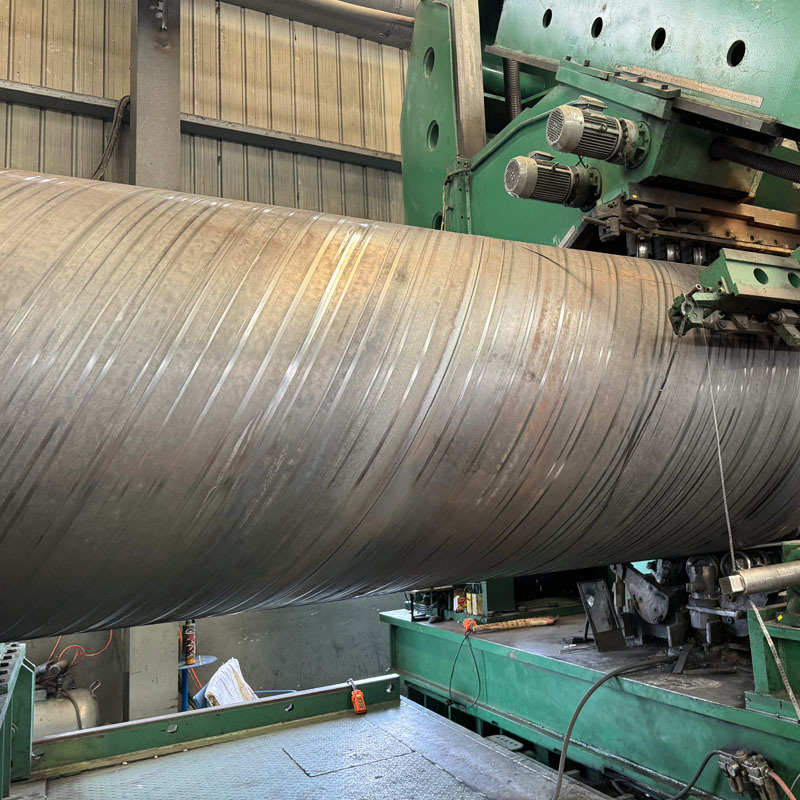
Advantages:
ERW PIPE:
1. ERW pipes are manufactured using high-frequency induction welding technology to reduce production time and costs.
2. ERW pipes can be produced continuously from coiled steel, thus achieving high productivity and rapid manufacturing.
3. The automated nature of ERW welding ensures consistent weld quality throughout the entire pipe length. Maintain high standards of dimensional accuracy and weld integrity.
4.ERW pipes have good dimensional accuracy, uniform wall thickness and excellent mechanical properties, making them suitable for demanding applications. Suitable for high pressure and harsh environments
5. ERW pipe is easily fabricated into a variety of shapes and sizes, including elbows, elbows, and T-joints.
6. ERW production produces less waste and reduces energy consumption, making it a more environmentally friendly option.
SAW:
1. SAW has a higher welding metal deposition rate, and it can produce thicker welds in a single pass.
2. The submerged arc process produces high-quality welds with good mechanical properties. Flux protects the weld from atmospheric contamination, thereby reducing weld defects.
3. SAW can achieve deep penetration of the workpiece and create a strong fusion between the base metal and the weld metal. 4.SAW is ideal for welding thicker steel, typically from 6 mm to several inches in thickness. It can effectively handle materials of various thicknesses.
4. SAW automation can be easily achieved using a welding tractor or robot to continuously weld long welds without frequent operator intervention. This automation increases productivity and reduces labor costs.
5.SAW usually reduces the deformation of the workpiece. This helps maintain the dimensional accuracy of the welded structure.
6.SAW Longitudinal welding (LSAW) and spiral welding (SSAW) of pipes produce consistent and reliable welds along the entire length of the pipe, ensuring structural integrity.
7. The submerged arc welding process produces less welding smoke and spatter, resulting in improved workplace safety and reduced post-weld cleanup.
8. SAW is cost-effective for large projects because of its high productivity, efficiency in welding thick materials, and high deposition rates.
Applications:
Welded pipes are used in various industries including oil and gas, construction, water supply, automotive, and manufacturing.
They are suitable for transporting liquids and gases under high pressure and temperature conditions.
ERW PIPE:
1.ERW pipes are widely used in oil and gas, water supply, structural, automotive and construction industries. They are available in a variety of diameters, thicknesses and lengths to meet specific project requirements.
2. ERW pipes are widely used in the construction of oil and natural gas pipelines that transport petroleum products, natural gas and other fluids. Suitable for onshore and offshore applications.
3. ERW pipes are widely used in municipal and industrial water supply systems.
4. ERW tubes are used in a variety of structural and construction applications such as building frames, bridges, towers and supports.
5. ERW tubes are used in the automotive industry to manufacture exhaust systems, chassis components and structural parts. They have a high strength-to-weight ratio and can withstand mechanical stress and vibration.
6. ERW pipe is commonly used in fencing and scaffolding applications. They are used for perimeter fencing, construction site barriers and temporary structures.
7. ERW pipes are widely used in a variety of mechanical and engineering industries to manufacture components such as conveyor systems, handrails, racks and brackets.
8. ERW pipe is used in buildings, bridges and marine structures.
9. ERW pipes are used in agricultural applications in irrigation systems, drainage systems and livestock pens.
10. ERW pipes are used in the mining industry to transport slurries, chemicals and tailings.
11. ERW piping is used in fire sprinkler systems in commercial and residential buildings.
SAW:
1. SAW is widely used in the manufacture of straight seam welded pipes (LSAW) and spiral welded pipes (SSAW). These pipes are used in oil and gas pipelines, water pipelines, structural applications, and other industries that require large diameter and thick wall pipes.
2. SAW is commonly used in the manufacture of pressure vessels such as boilers, reactors and storage tanks.
3. Submerged arc welding is used by shipbuilders to weld structural components of ships and offshore structures.
4. The SAW welding process is favored in the construction of offshore platforms, pipelines and subsea structures.
5.SAW is used in the manufacture of train cars, locomotives and other railway components. It welds thick sections efficiently, ensuring structural strength and durability for heavy-duty applications.
6. SAW is used to manufacture steel structural components of bridges. It facilitates the welding of girders and girders and helps build a strong and durable bridge structure.
7. Heavy machinery and equipment manufacturers use submerged arc welding to weld components such as frames, chassis and structural supports.
8. SAW is used in the manufacture of wind turbine towers. It enables efficient welding of large diameter cylindrical sections, ensuring the structural integrity and reliability of the wind tower structure.
9. SAW is used in the construction and maintenance of nuclear power plants, especially for welding components that require high integrity and resistance to radioactive environments.
10. SAW is used in a variety of infrastructure projects, including the construction of dams, power plants, sports stadiums and industrial facilities.
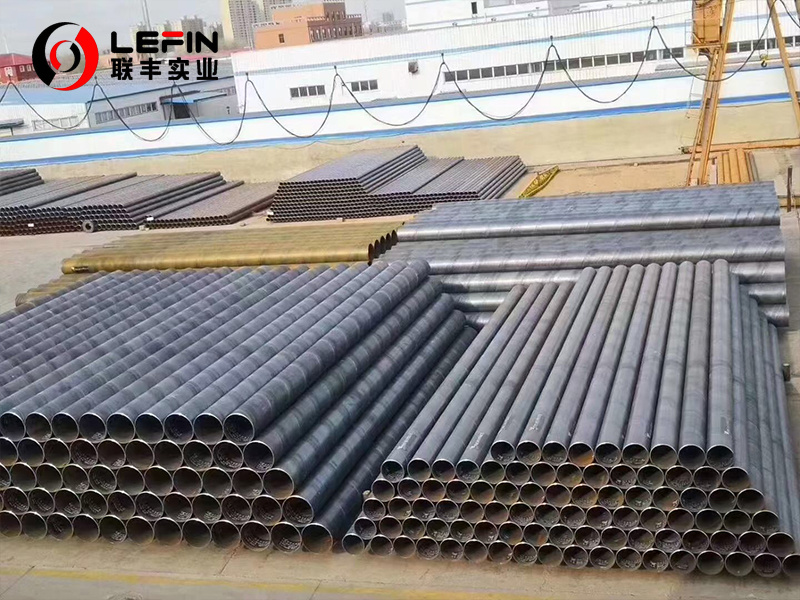
In structural applications, welded pipes are used for supports, columns, and other load-bearing structures.
In summary, welded pipes are a crucial component in various industries for their cost-effectiveness, reliability, and versatility in applications ranging from structural support to fluid transportation. The welding process used determines the characteristics and performance of the pipe, making it suitable for different operational requirements and environmental conditions.
Tags:
Relevant Project

Address: Hengtai Road,Daqiuzhuang Town,Jinghai County,Tianjin,China
Mob: +8615122229899(whatspp)
Phone: +86 22 58171905
Fax: +86 22 58171902
E-mail:info@lefinsteel.com
Get company updates

Tianjin Lefin Industrial Co.,Ltd. All rights reserved City sub-station SEO www.300.cn